The manufacture of concentrated juices is a key activity of TBF Group. The Company comprises 6 processing plants manufacturing concentrated, not-from-concentrate juice and fruit purées.

Maximum speed of interaction with customers and partners. Delivering to all locations around the world.

Ensuring quality through automated packaging equipment that meets the highest market standards.
Products
Technologies
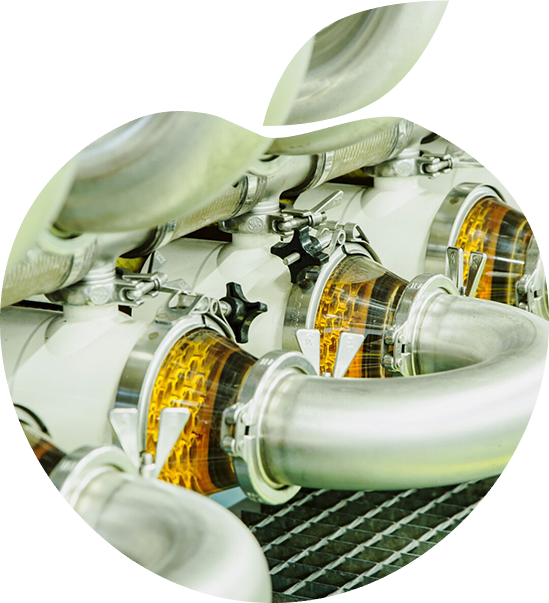

The TBF Group’s plants are equipped with high-tech lines and components from industry-leading manufacturers: Bucher, Boema, etc. Projects to modernize and expand production are implemented yearly.

One of the most important factors affecting product quality is water. We use water that has undergone a four-stage purification process (sand filter, ion exchange resin, carbon filter, reverse osmosis) at all stages of manufacture.

At the TBF Group’s plants, we have implemented a closed-loop manufacturing.

The refrigerated products are stored in 100m³ stainless-steel tanks in a clean, dry room at 0 to 10 °C, with no sudden temperature fluctuations and direct sunlight.
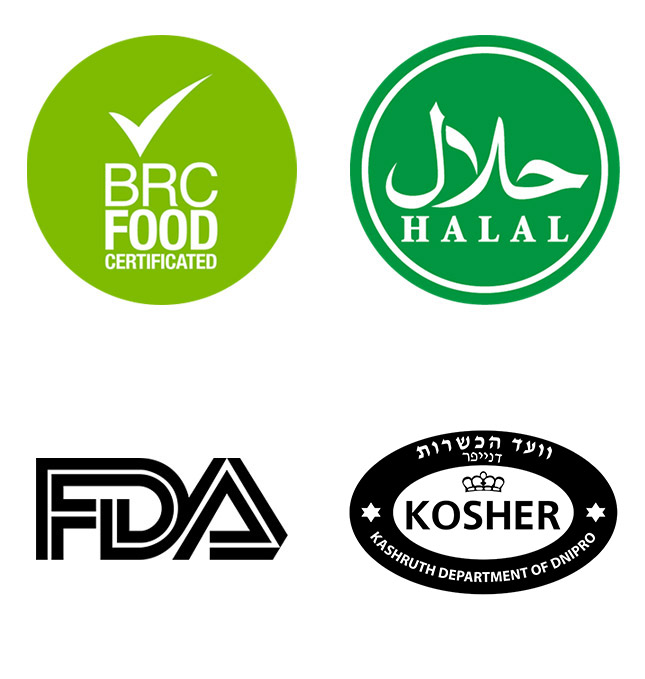
Quality system
The manufacturing facilities implemented a quality and food safety management system based on HACCP principles.
The Quality Control Department monitors compliance with the established standards at all stages of manufacture, from incoming inspection of raw materials and supplies to release of finished products. The safety and identity of the products are monitored by internal and external laboratories accredited under the national and international standards and operating in Ukraine and the European Union. The Company complies with Ukrainian and international legislation, as well as the requirements of BRCGS (Brand Reputation Compliance Global Standards), AIJN (European Fruit Juice Association), etc.
Given the Company’s expanding geographical reach, it is also responding to the customers’ specific requirements. For this reason, the Company has been certified to meet the requirements of the Jewish religion (Kosher) and Islamic food standards (HALAL).
FAQ
We always locate our plants in regions rich in the raw materials from which we manufacture our products. Each plant is located no further than 200 km from the sourcing base.
More than 40 professionals work on quality control in the Company, constantly receiving additional training. Each of the 6 TBF Group’s plants is equipped with its own advanced laboratories.
Having 6 plants in different regions enables us to provide a wide acidity range of products for our customers at a competitive price.
We sell our products all over the world.
The Company is constantly working on sustainable development and implementation of zero-waste technologies in manufacture. All plants implemented a closed-loop manufacturing that ensures full utilization of all raw material components.
Contact us
Give us a call at our phone number. Our team will provide you with answers to all your questions